Adhesives & EncapsulantsTM

About PLENSETTM
PLENSETTMis a one-component epoxy resin adhesive created based on the advanced
latent hardener technology that Ajinomoto Fine-Techno has cultivated over many years.
This product
employs a unique curing system using heat curing, UV curing, and combined UV/heat curing, and boasts
performance that sets it apart from other adhesives.
PLAIN SETTM achieves advanced properties
that conventional adhesives could not, demonstrating its capabilities in a wide range of applications such
as high-precision electronic components like camera modules, semiconductor packaging, and automotive
electronics.
Its advantages are particularly notable in the assembly of precision electronic components
and products where reliability is crucial.
These features not only enhance adhesive performance but also
significantly contribute to product reliability and process improvement.
Issues with industrial adhesive and encapsulating materials
Application
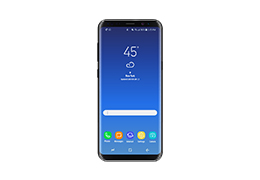
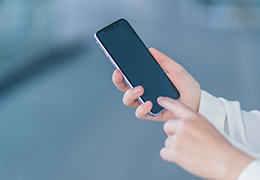
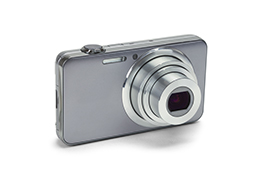

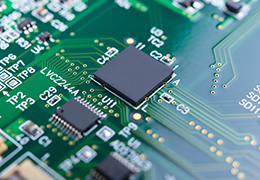
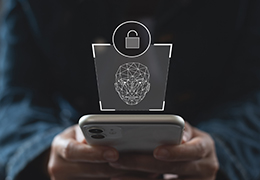
Resolve your issues with Ajinomoto Fine-Techno's core technologies
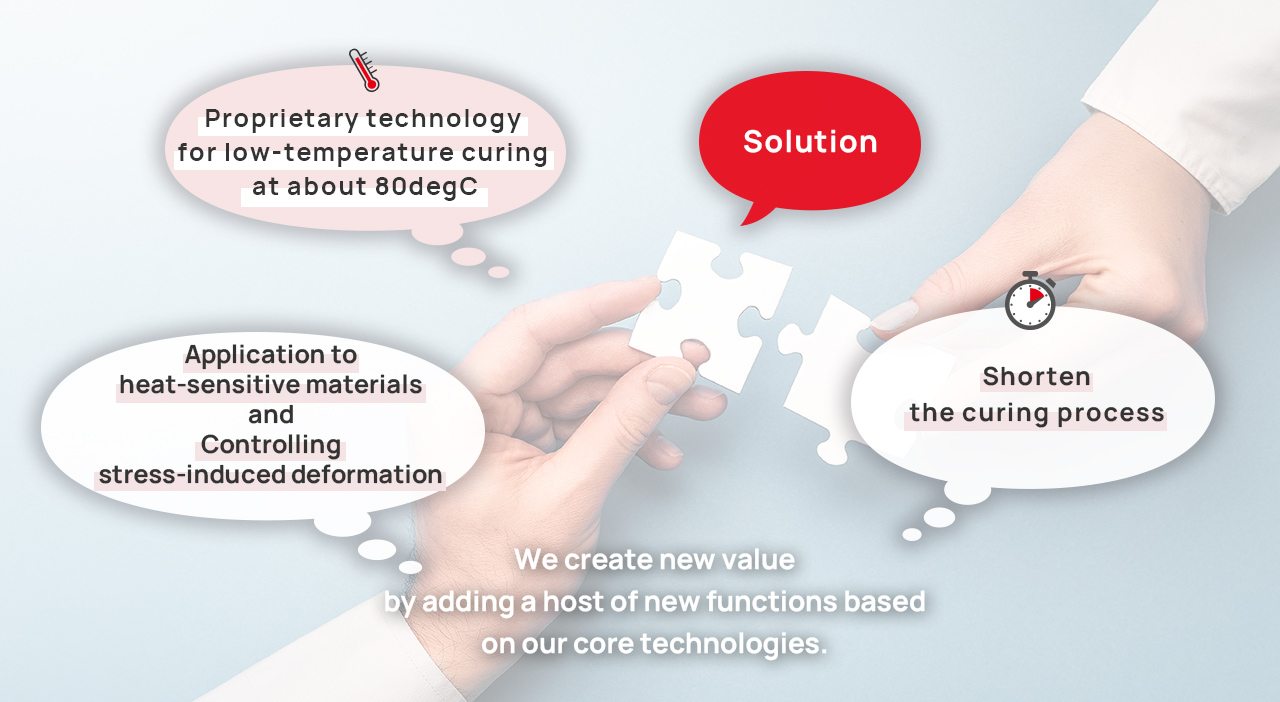
Product features and lineup
Insulation properties
- Unmatched low-temperature curing capability
- Low-temperature curing prevents warping and deformation
- Adhesion to heat-sensitive and precision parts
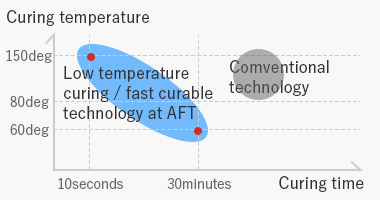
- Low-temperature curing at 80degC for 30 minutes
- Low elasticity enables superior stress alleviation and drop impact resistance
- Adhesion to dissimilar materials and vibration suppression
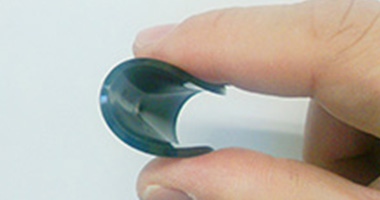
- Powder-free no particle type
- Impregnation bonding to narrow gaps possible
- Adhesive thickness reduced to surface roughness level
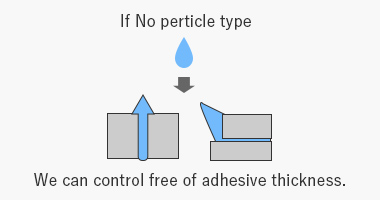
- Encapsulation possible even with narrow gaps and minute amounts of coating without uncured separation
- Application of no particle curing system
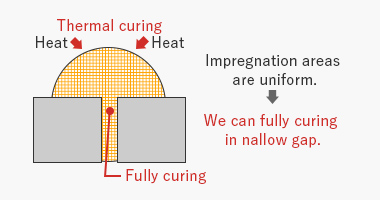
- Applications demanding higher reliability in terms of adhesiveness, toughness, and moisture resistance
- Fast curing at high temperature
- Applications for optical communication, 5G communication, in-vehicle equipment, and more
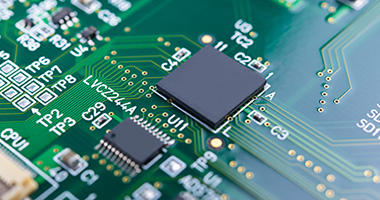
- Encapsulation possible even with narrow gaps and minute amounts of coating without uncuring separation
- Protective encapsulation against water vapor and other gases
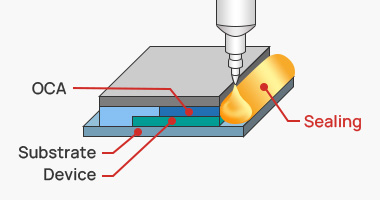
- Temporary fixing possible with UV
- Low temperature curing (80degC) by heat is possible for areas not irradiated by UV
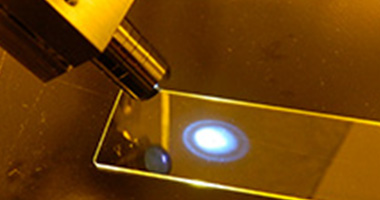
Conductivity
- Low-temperature curing at 80degC for 60 minutes
- Connection with heat-sensitive components
- Galvanic corrosion inhibition, solder alternative
- Application to wearables and flexible printed circuit boards (FPCs)
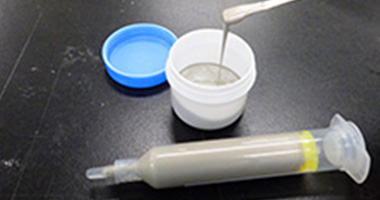
Developing products
- Compatibility of low-temperature curing and thermal conductivity. Curing possible in 30 minutes at 80degC
- Has flexibility curable 30minutes at 80degC => Superior drop impact resistance
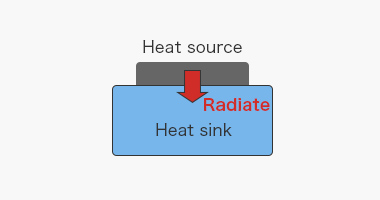
- Highly transparent cured material
- Low-temperature curing at 80degC for 30 minutes
- High resistance to UV yellowing
